Wear Protection Cast Basalt & Ceramic Tiles
Introduction
Cast Basalt
Weartech Solutions is a pioneer in the manufacture of Cast Basalt tiles and cylinders in India since 2005.
After selective quarrying, the volcanic rock is melted at a temperature of around 1500ºC and cast into molds or spun into cylinders. The castings so produced are then subjected to heat treatment cycles in special kilns to produce re-crystallized basalt. The product thus produced inherits inertness of parent material. Its micro crystalline, non-porous texture being denser and more homogenous than raw basalt, acquires exceptionally high abrasion resistance.
Technical Details
- Friction Resistance: As more material is passed over Cast Basalt, it gets polished up thereby reducing friction further. Cast Basalt improves in service after getting polished. Wetting also improves its performance in practical applications.
- Impact Resistance: Direct Impact Resistance at a perpendicular angle is low like all other ceramics, but it can be increased with proper installation by reducing the angle of impact. Cast Basalt can be used to mitigate sliding abrasion. Moreover, external impact strength of composite basalt pipe (enclosed in M.S. Shell) is always more than that of bare Ni-hard Pipe.
- Chemical Resistance: Cast Basalt is almost absolutely acid/alkali resistant (except Hydrofluoric Acid) and hence corrosion resistant.
- Weight and Sizes: Basalt Tiles are available in regular shape square of 200 x 200 x 30 mm thick, weighing approximately 90 kg/sq m; whereas bends and pipes are lined using Basalt Cylinders of various standard sizes from 50NB upto 500NB.
- Temperature: Cast Basalt withstands temperature up to 450ºC.
- Life: Life of basalt-lined pipe is estimated to be 7 to 10 times that of Cast Iron, and 3 to 4 times that of Ni-hard Steel.
Specifications
- Specific Gravity : 2.8 to 3.1 gm/cm3
- Compressive Strength: Minimum 4500 kg/cm2
- Hardness: 8 as compared to 10 of Diamond Moh’s Scale.
- Abrasion: 0.4 mm material loss (max.)
Applications area
- Thermal Power Stations: Raw Coal Chutes/ Hoppers, Feed Bunker/Coal Bunker, Ash Pits, Crushers, Bottom Ash, Disposal Slurry, Dust Lines/ Bends, Pipeline/Bends, Fly Ash. Trenches below Hopper and pipelines, Pulverized Coal Piping
- Cement Plants: Dynamic Air Separators, Raw Mill Ducts/ Chutes, Drag Chain Conveyor, Grate Cooler Housing, Air Separator/ Cyclones, Coal Handling, Coal Hopper/ Chutes, Cement Conveying, Slurry Lines/ Bends Lines/ Bends, Discharge Boxes / Bankers, Lime/Silica Hoppers/Chutes, Chain Conveyor Housing, Mixers/Nozzles, Coal Venturi, etc.
- Sinter plants: Coke sorting unit, Coal bunkers / sinter bunkers, Lime bunkers, Coke breeze, Sinter plant cyclones, Sinter plant flow conveyors, Iron slurry line, Thick slurry lines, Air lift pipes, Telescopic pipes, Granulated slag, Hot mill flume, etc.
- Coal Washery: Coal Washing Plants, Coal Transportation, Conveyor Chutes/Pipes, Floatation Cells, Media Sumps, Centrifuges, Cyclones, Sieves, etc.



Ceramic Tiles
High Alumina Ceramic
Weartech Solutions manufactures a wide range of high alumina ceramic liners such as tiles, special shapes and pipe sections which have high alumina content and wear protection properties. These liners are bonded on to steel surfaces and are extremely effective for prevention of wear and tear due to high particle velocity, impingement, abrasion and impact. They are extensively used for lining of equipment prone to severe wear in core sector industries such as cement, steel and power.
Weartech Solutions manufactures ceramic tiles in the form of weldable and pasteable tiles for installation at site as well as pipe sections of various diameters specifically for lining of fabricated pipes, bends and fittings for pneumatic conveying applications specially for conveying of pulverised coal in thermal power plants
Alumina powder after ball milling and spray drying is pressed and sintered at high temperature. This sintered product consists of dense alumina with hardness of approximately 9 MOHS, and can withstand temperature up to 1000ºC.
Technical Details
- Application: Ceramic Lined Bends are used for conveying material with high velocity and used for short radius Bend applications.
- Thickness: Tile thicknesses range from 6 mm to 50 mm.
- Size: Tube (cylinders) sizes range from 40 mm ID to 150 mm ID.
- Temperature: Withstands high temperature up to 1000ºC
- Resistance: Excellent resistance to impingement, moderate impact & High erosive and abrasive wear.
Specifications
- Alumina content: Min 85%
- Density: 3.3-3.7 gm\cc
- Compressive strength: Min 4500 kg\sq cm
- Flexural strength: Min 2200 kg\sq cm
- Hardness: 9 Mohs
- Water absorption: Nil
- Coefficient of thermal expansion: 7-9 x 10-6
- Abrasion by rubbing (material loss) : 0.1 gms.
- Jet erosion test: 0.05 gms.
- Maximum Temperature: 1000ºC
Applications area
- Pulverized fuel lines
- Orifice
- Coal Conveying Lines
- Ash Conveying Lines
- Lining of Bunker & Hopper
- Mill Discharge Valve
- Multi Port Outlet
- Coal Washery Sump
- Cyclones & Separators
- Ceramic Nozzles
- Inner Cones
- Venturi Vanes



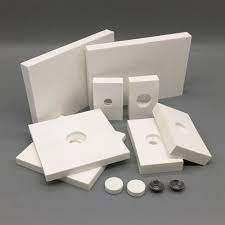

