Engineered Casting and Grinding Media
Introduction
Weartech Solutions an innovative manufacturing leader aims at bringing utmost standard with cutting edge technology, simplified systems and the most rugged and reliable equipment structure available. We are known for our engineered capability of delivering high quality products and solutions to all our customers.
Our Core strength
As an engineering company at heart with rich manufacturing capacity and technical application know-hows, our cumulative manufacturing capacity of delivering over 10,000 tonnes per annum of grinding media and castings advancements have over the years made our equipment excel in all challenging environments. Our engineers creates products that are catered to many leading Mineral Ore Dressing Units, Cement Plants, Thermal Power Plants, Railways, Steel Industries, Fertilizer Plants, etc. Each product improves their throughput, escalates their profitability, and condenses maintenance costs. We cohesively want our customers to be successful in their businesses, and will do all they can to provide you with products and solutions to do so in collective effort.
Our Team
Our team, comprises of engineers, technicians, administrative staff, each with vast expertise and industry experience. All we can comply with the highest and most stringent industry standards and focus on customer service and communication which assures unmatched and exceeded service experience. Our values completely thrive with each product produced and beyond. We ensure we offer complete support to our entire customer’s pre and post installation to ensure a seamless progression. Our expert crew stands with you throughout.
Our Initiatives
Abreast of development occurring round the clock, we strive to keep our ears to the ground and our focus on the developing pulse for all, we aim to continuously update our approach and prepare to leap in to influential industries to pave path ways. Ten of our technical experts are focused towards latest developments, enhancing product quality and on-time delivery, since we believe it is vital for innovation, competitiveness, contributions using latest technologies and high productive growth. We believe the manufacturing sector is evolving both in terms of opportunities and challenges and hence our range of inventory defines the purpose of all.
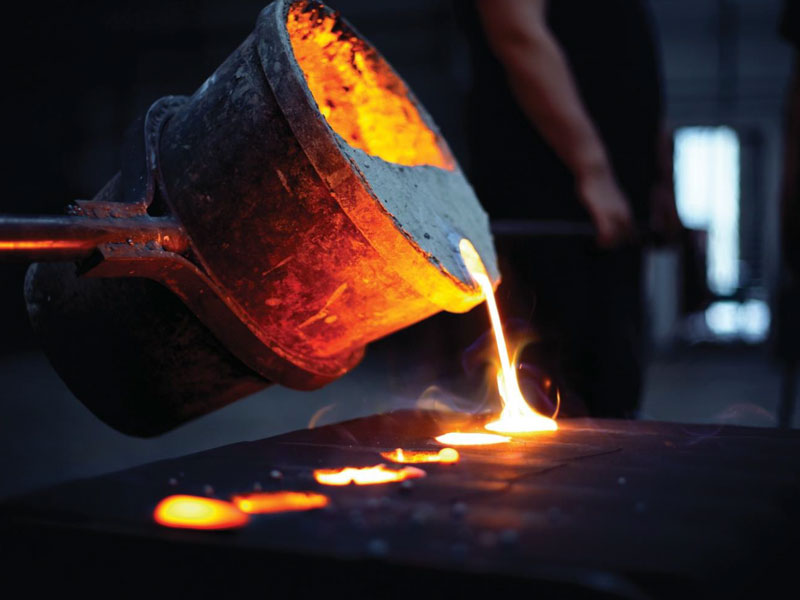
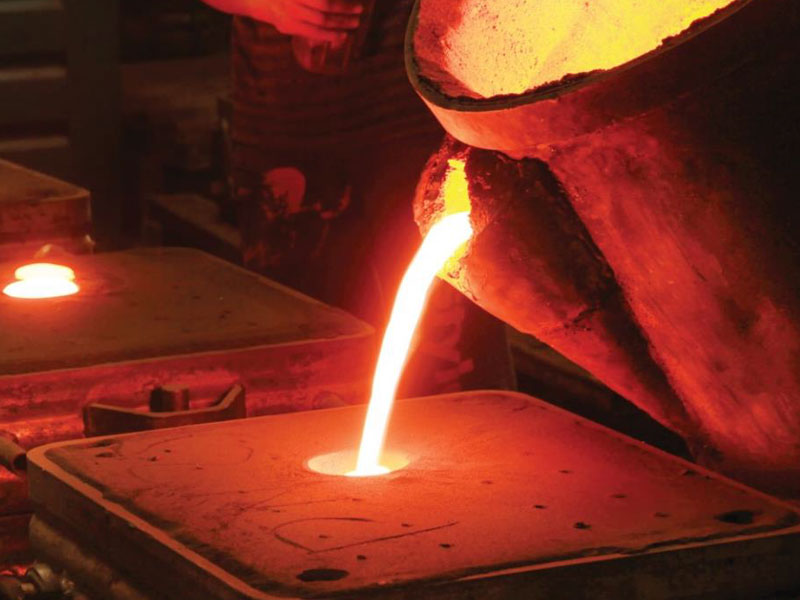
Grinding Media Balls
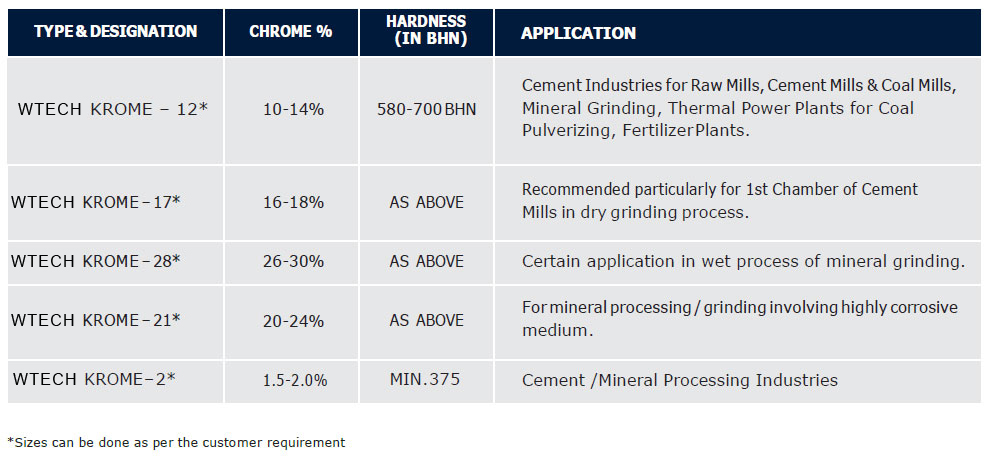
Features
- Variation of hardness from surface to core- ±1 RC Max
- Optimum level of chromium Carbides for reducing wear rate
- Retained Austenite’s – Less than 5% for avoiding microchipping
- Air Quenching Process
- Small batches of 200-250 kg.
- Quenching is done in rotating drums to all uniform cooling resulting to uniform hardness through section .
- Castings are free from internal defects due to special gating system
- Pouring – Done in 200 kg ladle for minimizing difference in pouring temperature of 1st and last mold resulting to uniform grain structure and consistent quality.
- Molding -100% Special CO2 sand used for perfect shape & free from sand inclusion
- Zone wise temperature Control in Heat treatment Furnace.
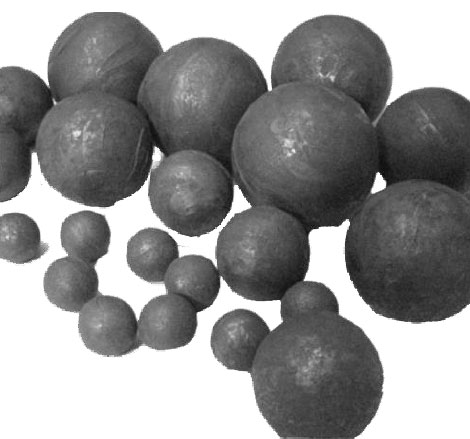
GRINDING MEDIA
Mill Lining System and Diaphragms
Features Diaphragms
- Self-supportive MS Structure.
- Large central opening for optimum ventilation
- Easy and tension free fixation block system for large diaphragm diameters
- Easy maintenance
- Tear of Bolts and protection concept
- Easy adjustment of the material flow control by adjustment flaps
- Active optimization by control of material level in the grinding chamber.
Type Of Diaphragms
- Intermediate diaphragm
- Discharge diaphragm
- Inlet diaphragm
- Double outlet diaphragm
Mill Linning System
- High Production Rate
- Low Specific Energy Consumption
- No Excessive lifting of the ball charge
- No ball impact on unprotected lining
- High Classification Efficient
- Full Functionality during the whole lifetime
- Maximum Grinding Chamber Volume
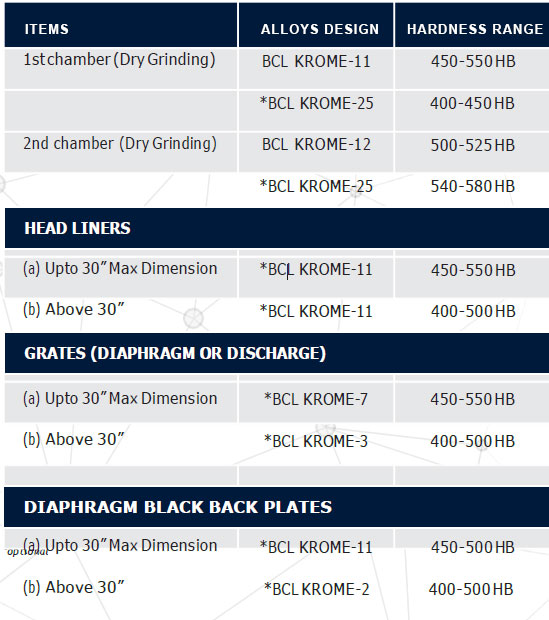
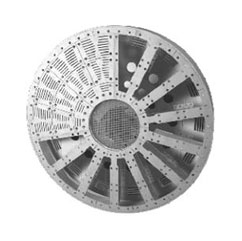
DIAPHRAGM FRAME
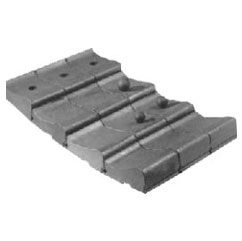
FIRST CHAMBER LINER
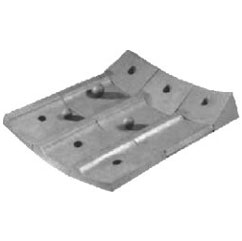
THIRD CHAMBER
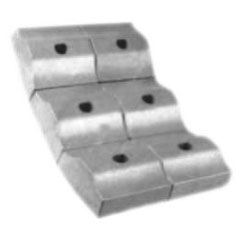
LINER 2ND CHAMBER
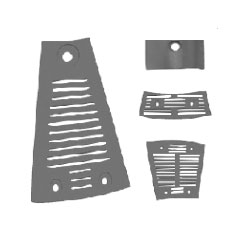
TYPE OF DIAPHRAGMS
Mn. Steel Casting
- Longer life and better production
- Less risk of premature failure
- Less downtime
- Guarantee for proper fit, performance and customer satisfaction
- Lower cost per ton of material produced
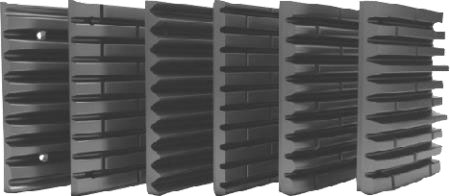
JAW PLATE
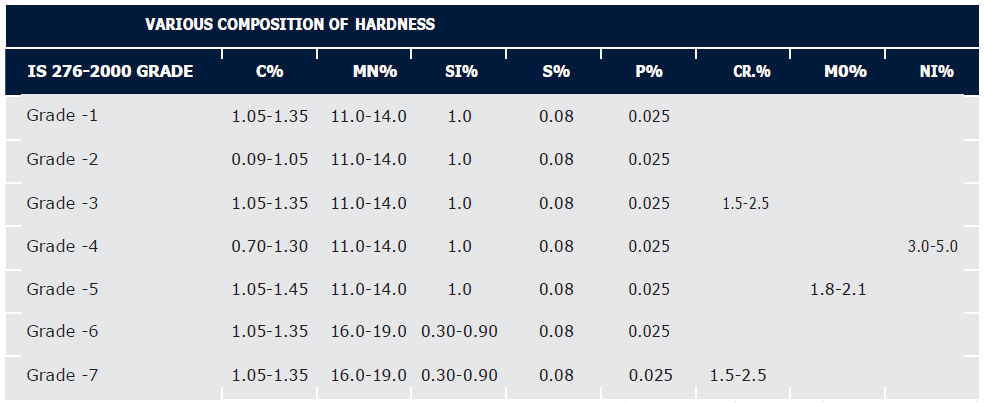
Products
- Concave And Mantle For Cone Crusher
- Spares for Jaw Crusher
– Side Plates
– Jaw Plates
– Toggle Plate
– Toggle Sheets - Paddle Arms And Tips For Hot Mix , Batch Mix
- Beaters
- Diaphragm
- Tooth point
- Blow Bar For HS-I
- Hammers
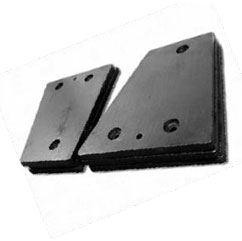
SIDE PLATE
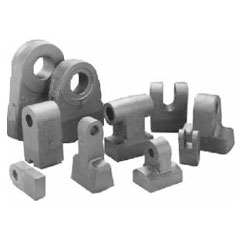
MANGANESE STEEL HAMMER
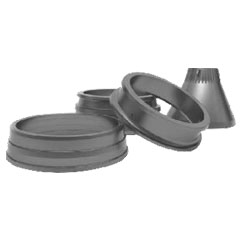
CONCAVE FOR CRUSHER
High Chrome Casting
Features
- Longer life on account of better wear resistance properties
- Less down time-lower operating cost
- Minimum specific wear and cost per tonne of material ground
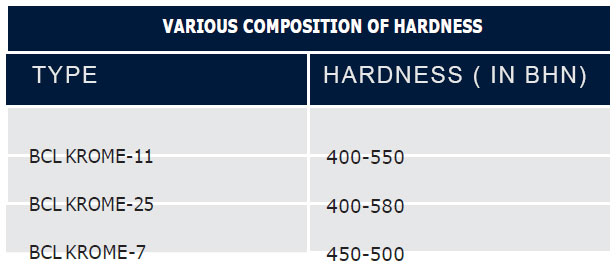
Products
- Liners and back plates
- Blow Bars
- Crushers Wear Plates
- Spares for Batch Mix, Hotmix Plant such as Paddle Arms, Tips Distribution Plants Liners
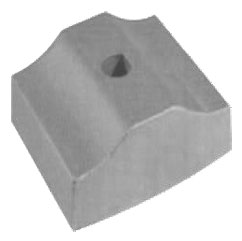
LINERS
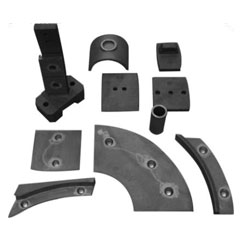
SPARES FOR BATCH MIX
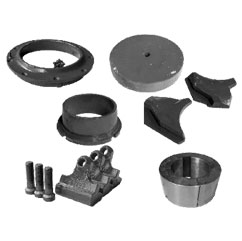
SPARES FOR VSI MACHINE
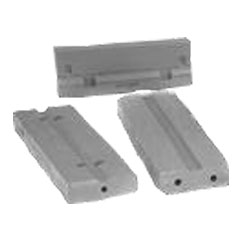
BLOW BARS
Facilities
Pattern Making
- Fully equipped to manufacture match plate mounted wooden, metallic and resin patterns to a high degree of accuracy
- Dedicated repairing section to minimise downtime
- In-house match plate mounting facility
- Measuring instruments that can produce accurate patterns
- Systematic pattern storage system of racks and powered mechanism to place individual match plates in allocated locations.
Moulding Facility
- Machine & hand moulding facilities
- Co2moulding to achieve consistent mould hardness in turn resulting to dimensional accuracy and to avoid foundry defects
- Besides co2 moulding, we have facilities for green sand moulding by preparing the sand on intensive rotor mixers, shell moulding
- Dry sand moulding depending on requirement of application
Melting Facility
- 3 inducto therm make medium frequency induction furnace of 750 kg each capacity
- 1 megatherm makes medium frequency induction furnace of 2 tons capacity.
Heat Treatment Facility
- Auto multizone continuous pusher type furnaces with multi-point temperature controlling with recorder and air quenching arrangement
- Tempering electric furnace, bell type with air circulation
- Batch type heat treatment furnace fully computerized 2T/batch
- Batch type Heat treatment furnece for Mn. steel Castings with multi – point temperature controlling along with the Recorder.
- Batch Size of 4Tons.
Testing Facilities
Physical Testing
- Microscope- Neophot Metallurgical Microscope with Camera and screen facilities- Carlzesis Germany make for Micro and Macro analysis Digital Image Analyzer for measurement of Retained Austenite, Carbide,Mertensite and Grain Size etc.
- Universal Testing Machine 40 T- For tensile , elongation, Bend testing
- Ball cutting machine- For Core Hardness.
- Portable Digital Hardness Tester
- Rockwell Hardness Tester
- Brinell Hardness Tester
Chemical Testing
- Spectrometer – Computerized Vacuum Emission Direct Reading Optical
- Spectrometer (Spectrolab Germany make) with accuracy of 0.001%,
- Ferrous background
Non Destructive Testing
- Ultrasonic Digital Depth Flow Detection Instrument.
- Magnaflux for Crack Detection.
- Dye-Penetration Test Equipment.

Our products meet the highest industry standards and are built using the latest technologies and advancements. We provide dealers and companies around the world with our dependable merchandise. No matter your needs, we have the right
solutions.